The ancient skill of weaving is thriving on the Clyde, and customers around the world can’t get enough of the fabrics made here
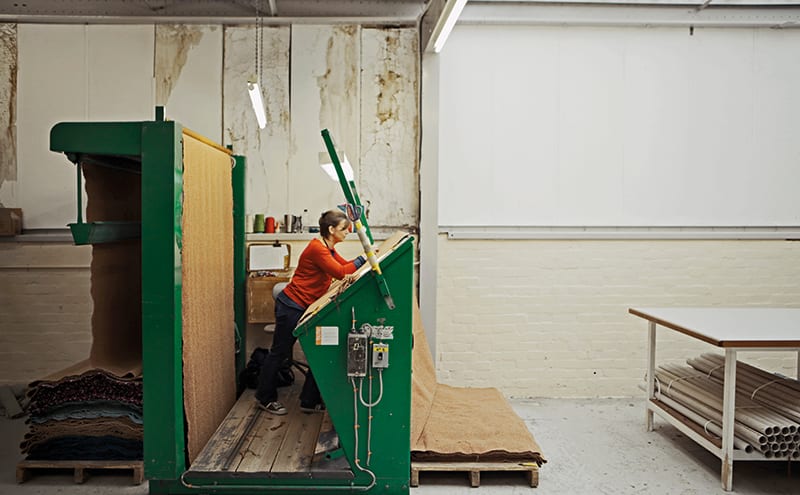
Let’s put that ugly neologism ‘staycation’ aside for a moment, because ‘doon the watter’, the old Glasgow expression, is more appropriate here. Catching the Calmac to the islands and towns along the Firth of Clyde is just as exhilarating now as it was for those escaping by steamer from the grime of factory work all those years ago.
The second-largest of the Clyde’s islands is Bute, and its sweeping beaches, heathery moorland and wild forests still pull in the day-trippers. It’s a fast and straightforward ferry crossing from Wemyss Bay railway station (itself an A-listed Victorian masterpiece, no less), which provides some of the old sense of escape. But there is more to the island than its dramatic landscapes and easy commute. Just beyond Rothesay, the main town, lies Bute Fabrics, a textile-producing powerhouse, where traditional warping, weaving and darning all take place.
Being on an island hasn’t held it back (“Orders can be dispatched to customers all over the world in a blink of an eye,” says communications manager Wendy Murray) and, in fact, location is a key component of the company’s story – along with how it survived dramatic economic volatility and changing social histories. As journeys go, this has been an adventurous one.
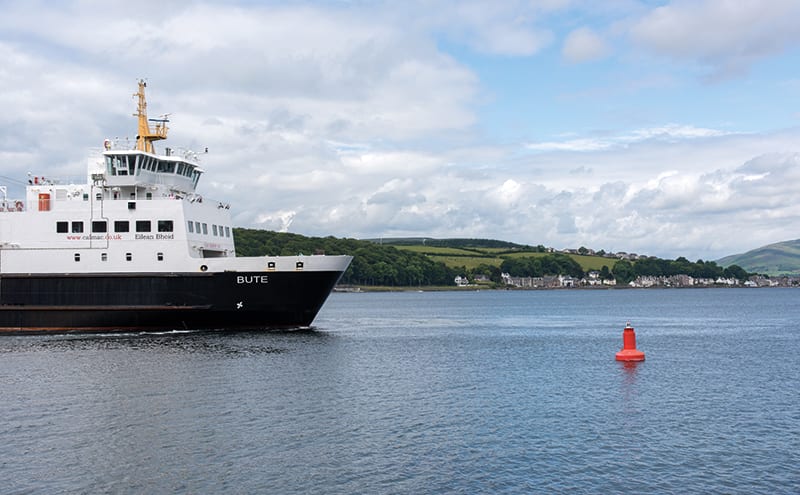
In its original incarnation, Bute Fabrics was a cotton-spinning mill, one of six on the island in the early 1800s. As industry declined with the onset of the American Civil War, southern ports were closed and cotton couldn’t be shifted. The subsequent dredging of the River Clyde allowed the cotton industry to move to Paisley, closer to Glasgow. The mill became an orphanage and a convent. By the late 1940s it was taken over by the 5th Marquess of Bute with the sole aim of providing employment for servicemen returning from the war.
Under a new name, Isle of Bute Industries, work commenced in the form of hand-weaving, leather-working and horn-carving. It wasn’t long before demand for most of these declined – although not for weaving, which took off. By the 1960s Bute Industries was producing hand-woven tweed fabric for French couture houses; later, under the name Bute Looms, it was weaving apparel for the larger market on power-looms.
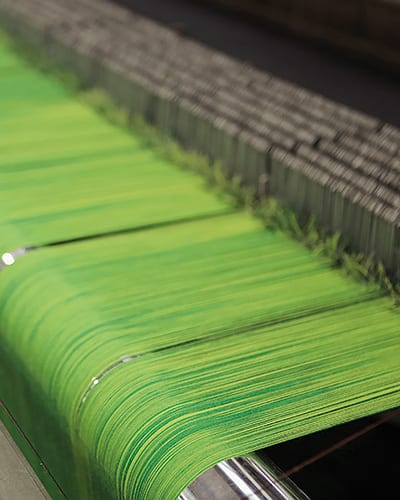
Soon, though, with the mass ownership of cars and central heating meaning fewer people needed heavy tweed clothing, it was time for another rethink. By 1979 the company had entered the American contract upholstery market, working with Herman Miller and Steelcase – two big furniture manufacturers in the US. Changing its name to Bute Fabrics, and with the aid of three commissioned weaving mills, it shifted 90% of production state-side.
Following the ’80s boom, its US business fell away and the company had once again to re-strategise. This time the target was architects and designers in the UK. It would also aim to reach a global audience by exhibiting at contemporary trade shows, such as the acclaimed 100% Design. Recruiting staff to market the business, which had, by this time, new purpose-built spaces in Bute (a weaving shed, yarn store and final-inspection room) and a refurbished and renovated mill, was absolutely imperative.
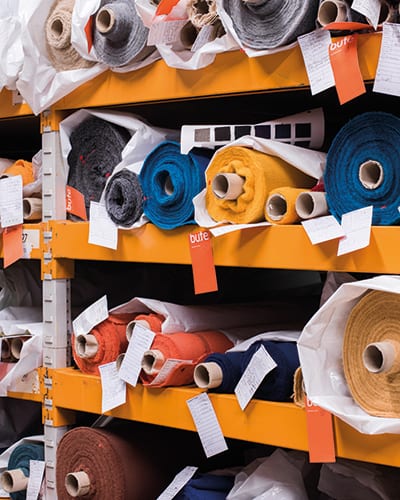
Today, as Bute Fabrics, all that reinvention has paid off, as has the investment in machinery and experienced personnel. Using natural fibres, the firm now weaves high-end luxury fabrics for domestic use to complement its global contract textile business.
“We’ve gone from strength to strength, cultivating markets worldwide and consistently pushing the boundaries of innova-tion,” says managing director John Glen. “To this day we’re supported by the Bute family and share in their continuing commitment towards the local community.”
Forty-eight staff, many of whom live on the island, turn the wheels of production. One, warehouse manager John Paterson, has worked here since 1983. “Because the mill is set in its own grounds, the local community rarely had an opportunity to engage with us,” says Glen.
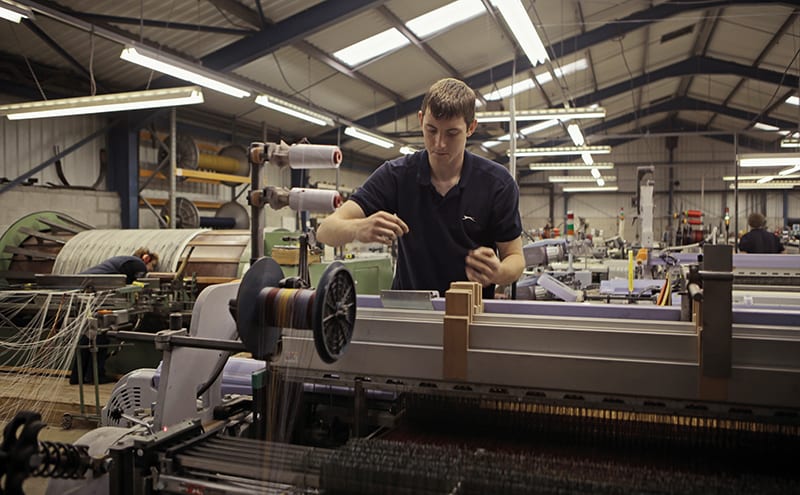
By way of welcoming all, the first Mill Open Day was held, with a great turnout of locals. It was followed up on a bigger scale in 2017, and this year’s is planned for August. The Atelier (part retail store, part workshop) across from the ferry terminal also links company and community.
In addition to this, engagement with local schools and colleges promotes positive opportunities for kids of all ages: a tartan design project with Rothesay Academy, for example, and the Bute Family Trust supporting its pupils to visit the Future Textiles training academy at Dumfries House, where they are taught sewing and trim-making using cloth from Bute Fabrics.
Since Glen was appointed in 2015, the biggest challenge he has faced has been updating a facility with aged machinery, and developing planned timelines for new products. “When I started, the company had not launched a Bute Fabrics range for seven years,” he says.
Now 20 years’ worth of redundant fabrics, machinery and office hardware have been cleared away, and the formal boardroom has been redesigned as a relaxed meeting space. Storage (the former dumping area) has been given a new lease of life and is due to become a modern showroom, with plans underway for a coffee and fabric shop.
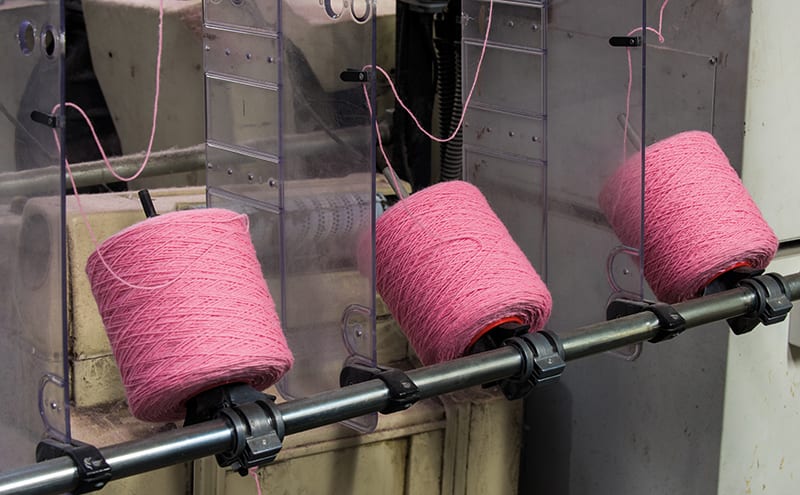
On top of a portfolio of work that includes projects for the Royal Festival Hall, the Queen’s Gallery and Hong Kong airport, the seven-year itch has produced exciting collaborations with homeware designers – big names in decor such as Tom Dixon, Barber & Osgerby and Patricia Urquiola among them.
Work continues at the mill, developing the brand, showcasing current and past projects to a wider audience, and investing in equipment. Two jacquard looms have been installed, which is opening up many new possibilities. In their basic form, these looms act like giant printers and can take ornate and complex visuals and translate them into woven fabrics, either as repeats or as one large image.
Bute Fabrics itself is a bit like an exquisite piece of cloth with the romance of Scotland and the island’s changing landscapes woven through it. “The ready-made palettes of vibrant colour and texture that surround us provide a continual source of inspiration,” says Murray.
DETAILS
Photography MakeWorks and Gordon Burniston
Words Gillian Welsh