Her parents set up Crail Pottery from a caravan in their East Neuk garden in 1965. Now, this talented potter has continued the colourful, creative passion of her family’s business
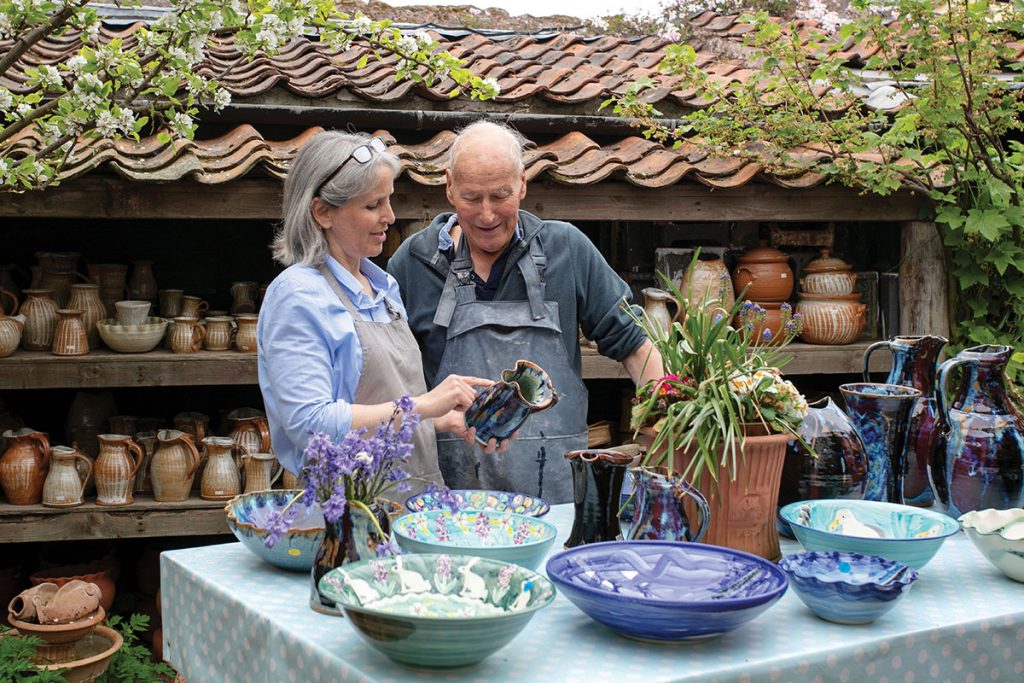
You can’t choose your family, but, if you have the option, you can choose whether or not to work with them. It’s what Sarah Grieve Mills did, joining her parents at their business, Crail Pottery.
In the heart of Fife’s East Neuk, Crail Pottery occupies two buildings arranged around a quaint courtyard filled with trees and flowers; one of them, with crowstepped gables and a pantile roof, is the oldest in the picture-perfect idyll, dating back to 1650. “On sunny days it feels like a little piece of the Mediterranean,” says Sarah.
“People can rest a while in the peace and enjoy looking at the pots on display.” A quietly comforting hum of activity comes from the two workshops: pots are being decorated, finished designs are being carried on planks to the kilns, clay is being prepared in the old dough mixer.
Sarah grew up here. Her parents, Stephen and Carol Grieve, ran the pottery and she spent all her time there. She vividly remembers standing on a chair (it’s still in the workshop now) beside her mum as she weighed out balls of clay that would be formed into mugs. “Once I was big enough, I would sit on the wheel and make pots myself. Dad would centre the clay for me and put a brick under the pedal, which controls the wheel speed, as I couldn’t reach it with my foot. I’d then make some pretty dodgy creations! I loved it, though. It’s all I’ve ever done.”
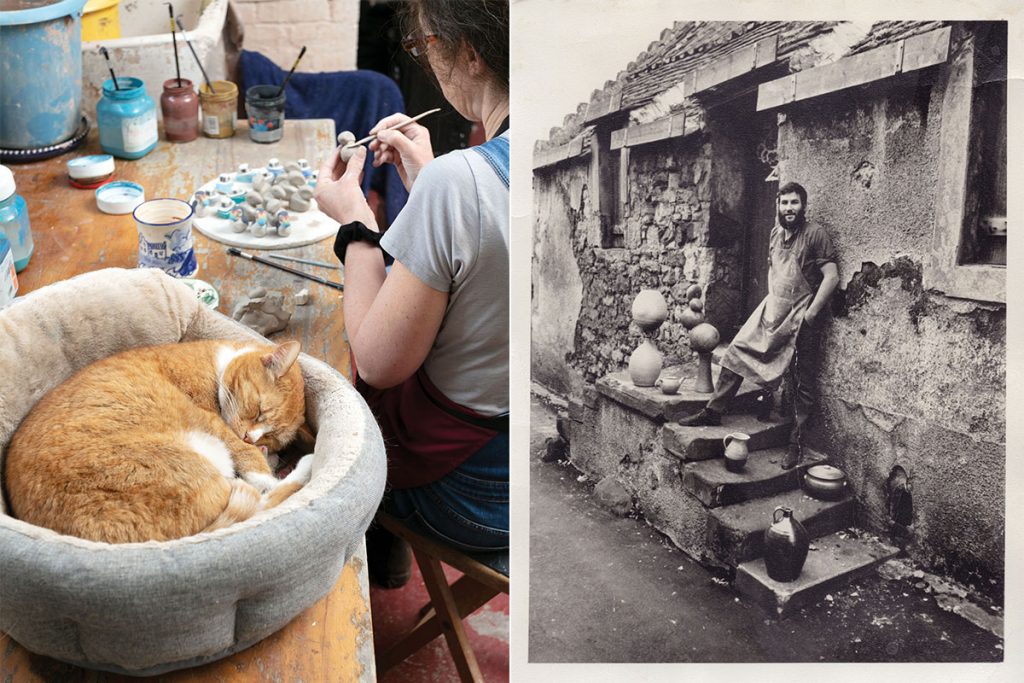
Sarah has made pots from the age of four and has been a full-time potter since she was 18. She spent a year in Australia but returned, satisfied that Crail was in fact the nicest place in the world. “My parents taught me to be a potter. I guess I got my degree in pottery from them.”
The pottery hasn’t changed much in its practice since it began – people have been making pots at the wheel for a long time, after all. The big change from the early days is that Crail now has electric wheels and kilns. It has allowed the business to be far more productive. It has expanded too, though it’s still a family co-operative: Sarah’s brother Ben runs Crail Earthenware with his wife Jane and their son Timothy. There’s Sarah’s ceramic line too, and the original Crail Pottery is still going strong with Stephen at the helm, since Carol sadly died earlier this year.
“We all have different ideas, which is why we have our own businesses – it encourages entrepreneurship as well,” explains Sarah. “It also helps with family unity. Each business does its own thing, producing different ranges of pottery, using different techniques.”
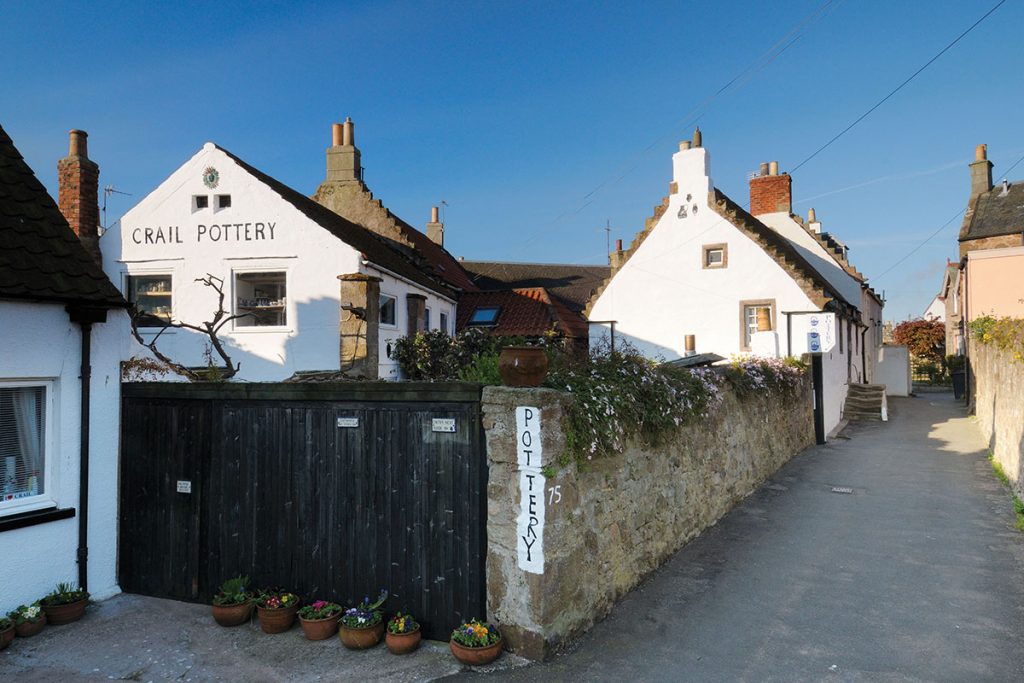
Stephen’s work is mainly gas-fired stoneware, using glazes he has spent a lifetime developing. Ben makes the popular ‘cooking pot’ range as well as North Sea Blue, along with Jane’s hand-painted thistle, tartan and bubble designs. Sarah’s pots are made using a white semi-porcelain clay that shows off the vibrant colours of her hand-painted East Neuk, Blue Rose and Hebrides lines.
A lot of equipment and space is needed in a pottery. There are four wheels, seven kilns, tables to glaze on, spaces dedicated to decorating, planks for the freshly made pots, areas for drying, for colours and paint brushes, and for finished work. There’s also an area to accommodate tons of clay, of which there are various types: earthenware, stoneware, raku and porcelain.
“We buy in bulk, mostly from the potteries in Stoke on Trent and Ireland, often getting deliveries of five tons of clay at a time. We get through around ten tons a year between us. You have to be strong to be a potter. There’s endless lifting to be done.”
Carol and Stephen started the pottery in 1965, inspired by British potter and art teacher Bernard Leach and by the beauty of the East Neuk. The idea of a pottery had come to them on a day out. Stephen was at university and Carol went to St Andrews to visit him. She was 18, he was 21. They took a bus trip to Crail on a beautiful day, falling in love with it instantly. “It was mad. They didn’t know how to actually make pots,” says their daughter.
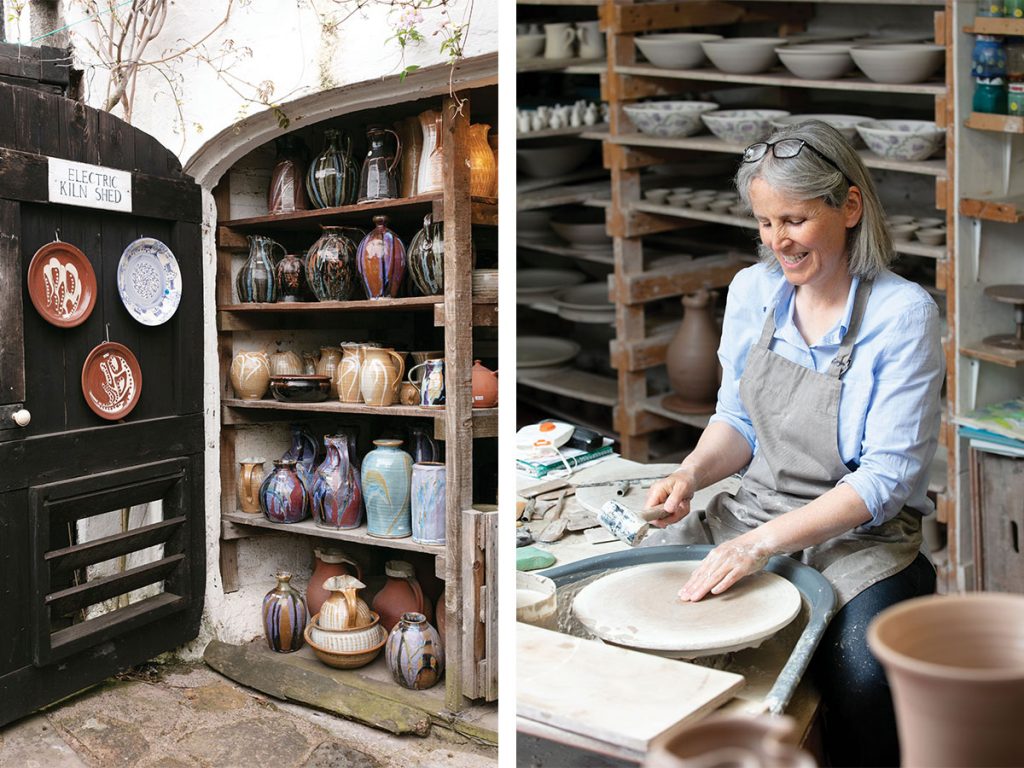
They managed to buy the two derelict buildings that now house the pottery for £250, a ridiculously cheap sum, even then. They got married, bought a tiny caravan and put it in the yard, slowly restoring the buildings while creating their business and, soon after, their family.
Now three generations work here, making a diverse range of designs. Visitors to the studio watch it all in progress. “Some of them become totally engrossed. We even have the occasional spontaneous round of applause when a particularly large piece is finished,” smiles Sarah.
Customers come from far and wide. As well as the loyal locals, who buy wedding presents, there are lots of Americans, partly because of the golf in the area, and visiting academics linked to the university. Graduation is very busy every year, as proud parents buy their off-spring a special reminder of the area. And the various festivals in the East Neuk bring in fresh waves of tourists throughout the summer.
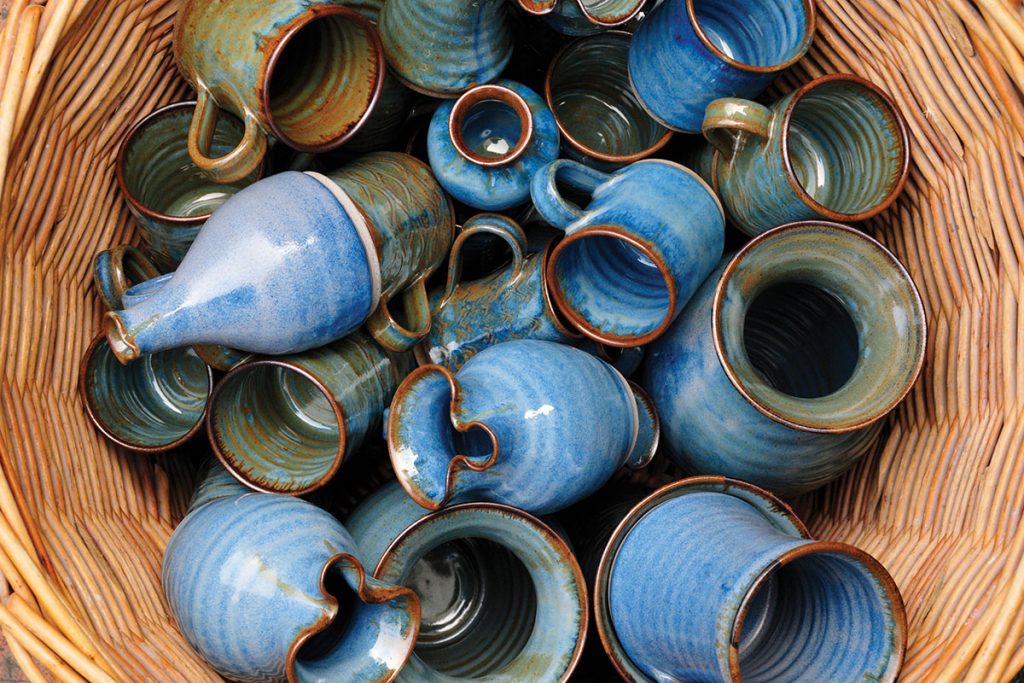
“One of our neighbours visited the Falkland Islands recently and when she got back she told us that she’d seen one of our pots in the Port Stanley post office. Other friends visited a remote island off Australia and found a complete Crail Pottery dinner set in the kitchen. They couldn’t believe it.”
Depending on its size, it can take up to three weeks to finish a pot. There are many processes to go through, from clay preparation, throwing, finishing, drying, painting and glazing to firing in the kiln – twice. Different clays are fired in different ways, with different fuels giving different results. Stephen’s pots, decorated with his unique glazes, are mainly gas-fired. Sarah’s are decorated with ceramic colours and then covered in a clear glaze and fired in the electric kiln. Ben does a bit of both.
“I think my favourite part is the throwing – I love to create a beautiful pot out of a lump of clay,” says Sarah. “It’s very satisfying to see all the pots that have been produced at the end of a day’s throwing. Some days, decorating is my favourite thing, especially if I’m a bit tired or stressed. I can just sit quietly and do a repetitive design. It’s relaxing.”
For a long time, anything painted or glazed blue would fly off the shelves. Surrounded by the blue sea and a big blue sky, that’s no surprise. Recently, though, Sarah’s green glaze has overtaken the blue. Greens and blues work well together; they’re safe to use too, unlike reds and yellows, which are notoriously difficult as they bubble in firing and are quite toxic.
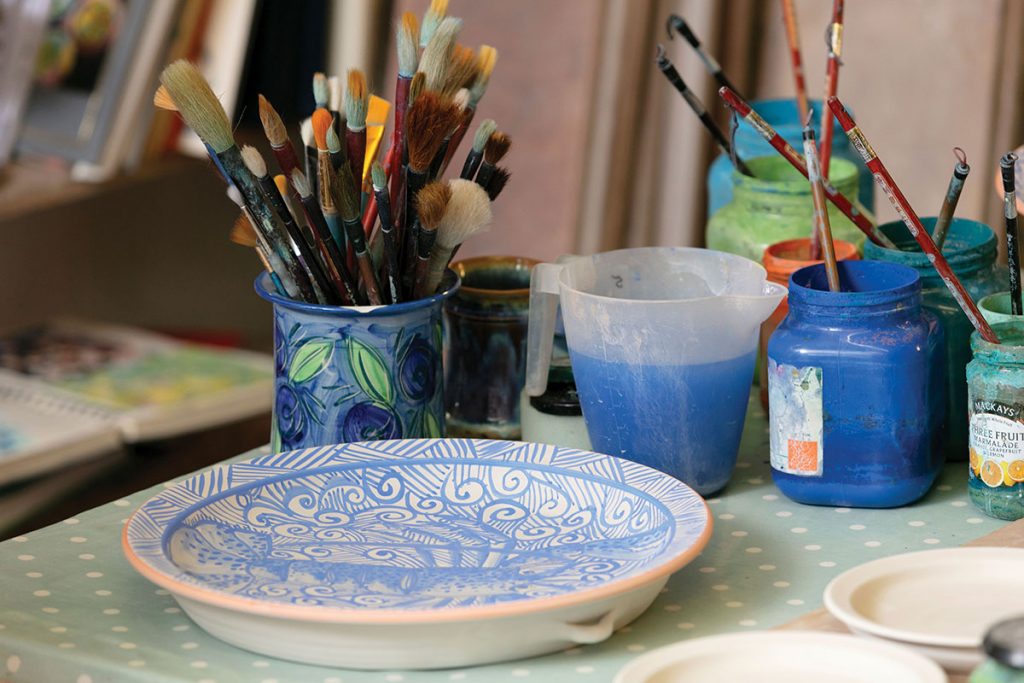
There are numerous health risks associated with pottery. Potter’s Lung is a disease caused by breathing in clay dust, so mopping floors to keep it to a minimum is a regular chore. Potters often suffer from a bad back as a result of all the lifting and time spent on the wheel. “And we have to be careful with our kilns as there is a risk of fire: many a pottery has burned down!”
The impression is of how relaxing this job must be, but a huge amount of effort is required to make a living. Around five thousand pots a year are made here. “We are human pottery-producing machines. It’s hard work.”
In summer, salad sets and platters are top sellers; in autumn, as the nights draw in, candles and lamps do well. Mugs are bought up in their hundreds, perhaps thousands. “I do feel I’m always chasing my tail to keep up with demand, so I guess that does stunt creativity a bit. I could do with a few weeks of experimenting and making things that I’ve never made before.”